La génération de plasma sous basse pression offre d’immenses opportunités de rendre la production de produits du quotidien plus durable et plus saine. Entretien avec Jody Paulus, CEO d’Europlasma.
Texte : Joris Hendrickx
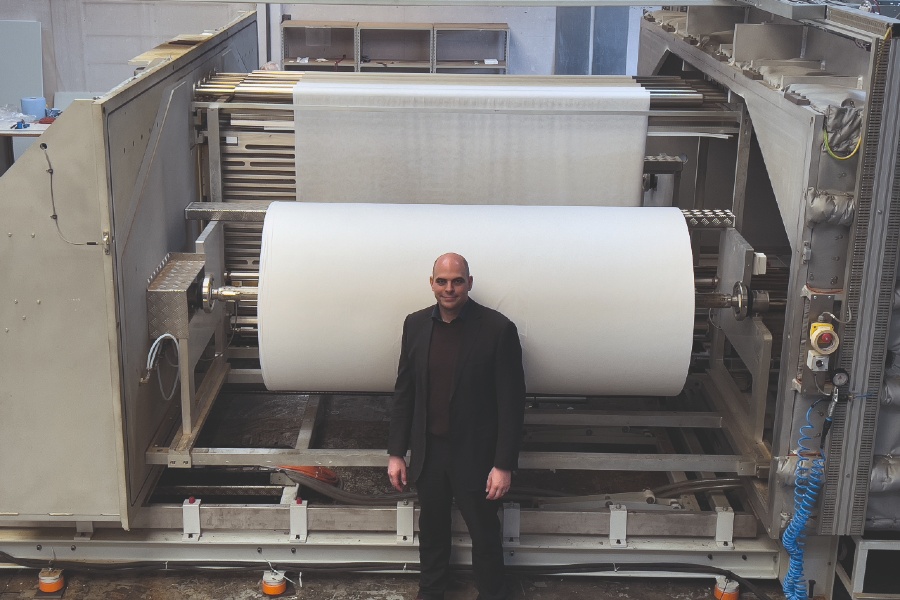
Pourquoi est-il intéressant de générer du plasma sous basse pression ?
Jordy Paulus : « Le plasma est généralement obtenu en fournissant de l’énergie (à température très élevée) à du gaz, jusqu’à ce que ce dernier atteigne un état d’ionisation. Europlasma, cependant, ne génère pas du plasma sous haute température, mais sous une pression extrêmement basse. En effet, sous basse pression, vous n’avez pas besoin d’une température aussi élevée pour obtenir le même état. Nous pouvons ainsi générer du plasma à une température d’environ 40 °C et, de ce fait, travailler avec des matières sensibles qui ne supportent pas une chaleur élevée. »
Quelles sont les applications ?
J. P : « La fabrication d’appareils auditifs est une application typique de notre technologie. Nos revêtements rendent ces appareils parfaitement étanches et résistants à la sueur. Tous les revêtements hydrophobes et oléophobes appliqués actuellement sur la plupart des composants électroniques sensibles contiennent du fluor, qui renferme lui-même du PFOS nocif. C’est pour cette raison qu’il y a quelques années, nous avons commencé à développer un revêtement qui offre ces mêmes fonctionnalités, mais qui ne contient aucun halogène.
Grâce à notre technologie, nous pouvons placer des rouleaux de textile entiers dans une grande chambre sous vide, puis appliquer notre revêtement.
« À la fin de l’année 2019, nous avons ainsi obtenu le revêtement électronique que nous souhaitions. Les six plus grands fabricants d’appareils auditifs sont désormais en phase de test notre revêtement sans fluor. Et l’un d’eux a déjà passé une commande. »
Les normes en matière de sécurité et de santé sont de plus en plus strictes. Le scandale récent de la pollution au PFOS à Anvers, en particulier, a fait considérablement augmenter la sensibilisation à ce problème. Nous espérons que les esprits sont désormais assez mûrs pour qu’il devienne obligatoire d’éliminer ces substances nocives de l’électronique destiné au grand public. Quelques grands acteurs du marché s’y emploient d’ores et déjà. »
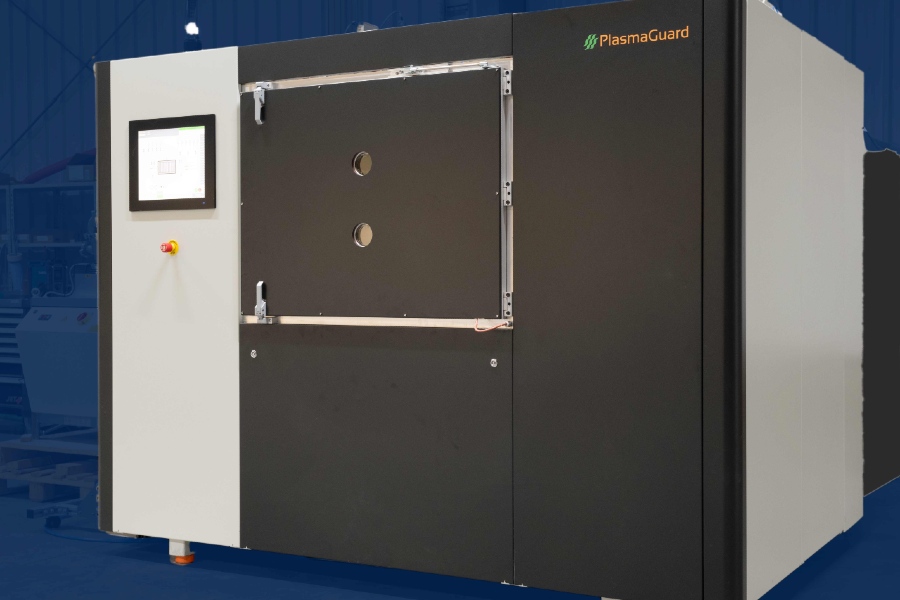
Où voyez-vous d’autres opportunités ?
J. P : « Nous pensons que notre technologie appliquée aux rouleaux aura un grand impact. Nous pouvons placer des rouleaux de textile entiers dans une grande chambre sous vide, puis appliquer notre revêtement. Il s’agit surtout ici de textiles techniques utilisés, par exemple, pour la filtration de l’air. Pour la fabrication de masques FFP2 et FFP3, ainsi que de filtres à air dans les voitures, les habitations et les bureaux, un revêtement oléophobe est d’abord appliqué sur le textile. Ensuite, ce textile est chargé électriquement, de sorte qu’il attire certaines particules présentes dans l’air.
« L’innovation réside toutefois dans le fait que nous n’utilisons plus d’eau potable pour cette opération. Nous injectons un gaz dans la chambre, puis nous appliquons une pression extrêmement basse afin qu’il se transforme en plasma qui adhère au textile. Il n’est plus nécessaire d’effectuer un trempage dans des bains de produits chimiques contenant du fluor, des solvants et de l’eau. Ce processus chimique est malheureusement très polluant, car l’eau doit ensuite être déversée. C’est précisément le problème actuel à Anvers : cette pollution chimique de l’eau n’est pas biodégradable et persiste donc éternellement dans la nature. »
Un avantage important supplémentaire est que nous utilisons des nanorevêtements, plusieurs centaines de fois plus fins que les revêtements classiques dont je viens de parler. Nous limitons ainsi non seulement la quantité de substances chimiques nécessaires, mais nous réduisons aussi les déchets de 95 %. Nous diminuons également les émissions de CO2 de plus de 80 %. Tous les gaz excédentaires sont pompés et collectés par des filtres à air qui, en tant que déchets chimiques, sont confiés à une entreprise de traitement agréée. »
À quoi pouvons-nous nous attendre à l’avenir ?
J. P : « Actuellement, nos rouleuses tournent à une vitesse de dix mètres par minute, environ. De nombreuses machines sont donc nécessaires pour assurer la totalité d’une production. L’année prochaine, nous lancerons dès lors un concept entièrement nouveau, qui permettra à nos machines de tourner quatre fois plus vite. Nous pourrons ainsi desservir une plus grande partie de l’industrie. L’Agence européenne des produits chimiques nous a d’ores et déjà désignés comme une des deux entreprises offrant une alternative de qualité dans ce cadre. »